Металл, разливаемый непрерывным способом и в изложницы, должен иметь температуру в заданном узком диапазоне. Чтобы попасть в этот диапазон, металл в ковше подогревают или охлаждают различными способами. Наиболее экономичным способом подогрева является химический подогрев. Химический подогрев стали осуществляется теплом, выделяющимся при реакции окисления алюминия. Для этого сначала в ковш вводят алюминиевую проволоку с помощью трайбаппарата, а затем подают через погружную фурму кислород. При этом для ускорения процесса, усреднения химического состава и температуры стали проводится продувка аргоном. При совершенствовании технологии химического подогрева возникают вопросы, связанные с выбором расхода алюминия, параметров продувки (расхода и продолжительности, момента подачи) кислородом и аргоном.
Для ответа на эти вопросы была разработана математическая модель процесса химического подогрева стали в ковше [1]. Модель включает описание четырех взаимосвязанных процессов, происходящих в объеме металла:
1. Теплопередача в системе «металл футеровка шлак окружающая среда».
2. Диффузия алюминия.
3. Диффузия кислорода.
4. Химическая реакция окисления алюминия.
При описании этих процессов предполагалось, что ковш имеет цилиндрическую форму, а распределения температуры и концентраций симметричны относительно оси ковша (рис. 1). Теплопередача в металле и шлаке осуществляется путем теплопроводности и механического переноса с потоками метала при свободной и вынужденной конвекции (продувка аргоном и кислородом). Охлаждение металла происходит за счет теплопередачи от металла через днище, стенку ковша и шлак к окружающей среде. Считаем, что в начальный момент времени вся масса введенного алюминия распределена в ограниченной области, центр которой расположен на оси ковша. Кислород подается и распределяется в области, центр которой также расположен на оси ковша. Области расположения алюминия и подачи кислорода могут не совпадать по размерам и месту расположения максимумов величин. Перенос кислорода и алюминия в жидкой стали происходит путем диффузии и механического переноса при свободной и вынужденной конвекции металла в ковше. Химическая реакция окисления алюминия ограничена только доставкой кислорода к месту реакции.
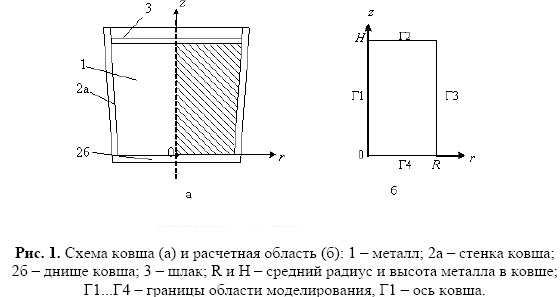
Система уравнений, описывающих приведенные процессы с соответствующими начальными и граничными условиями решена численным методом конечных разностей. Решение каждого дифференциального уравнения протестировано. Связь между эффективными коэффициентами тепломассопереноса и энергией вдуваемых газов адаптирована по экспериментальным данным [2], полученным по выравниванию химического состава стали в ковше при продувке аргоном.
Модель использована для имитации процесса подогрева стали 350 т в ковше на УДМ: исходные данные для моделирования: G = 350000 кг, сталь 08Ю, Т0 = 1863 0К, начальное содержание алюминия [Al]=0,05 %, усвоение кислорода и алюминия 50 %.
На рис. 2 приведены результаты моделирования по динамике подогрева металла при химическом подогреве для двух вариантов: 1 при расходе алюминия AAl=142 кг и продувке кислородом с интенсивностью I=0,5 м3/с в течение tO2 =180 с; 2 при расходе алюминия AAl = 250 кг и продувке кислородом с интенсивностью I=0,625 м3/с в течение tO2 =240 с. Продолжительность усреднительной продувки аргоном после продувки кислородом составляла для обоих вариантов 180 с.
Как видно на рис. 2, подогрев стали или повышение средней по объему металла температуры составило около 10 0С для первого варианта технологии и около 20 0С для второго. Полученные результаты хорошо согласуются с производственными результатами.
В результате неравномерной по объему металла подачи алюминия и кислорода возникает неравномерность по температуре и химическому составу, которая уменьшается в процессе усреднительной продувки. На рис. 3 и 4 приведены результаты моделирования снижения химической неоднородности по алюминию и перепаду температуры в ковше при химическом подогреве.
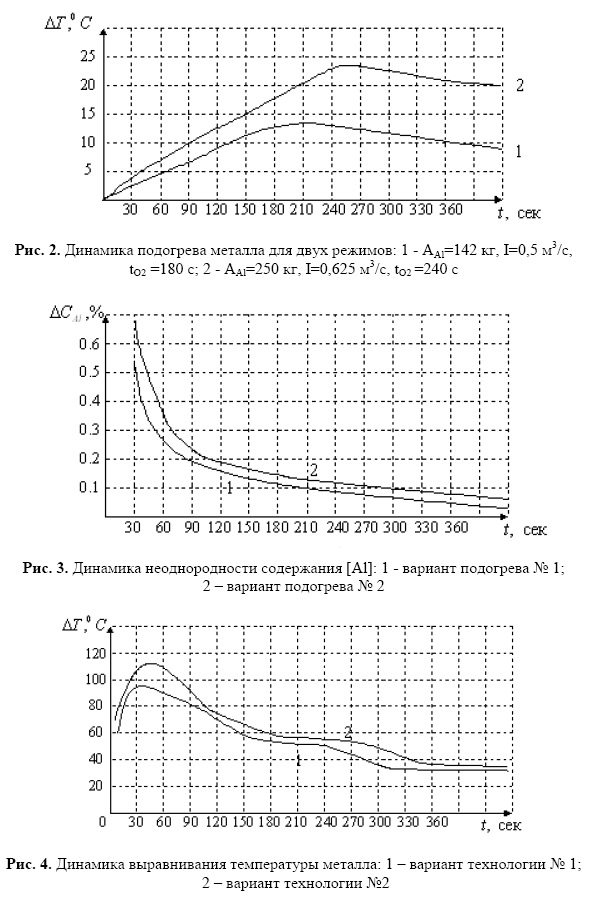
Из рис 4 следует, что перепад температуры стабилизируется уже к 360 сек после ввода алюминия и усреднительной продувки и достигает остаточного значения 3035 0С для обоих вариантов. Последнее значение перепада связано с охлаждением металла через шлак и футеровку ковша.
С целью совершенствования технологии изучили влияние продолжительности продувки кислородом, интенсивности и момента начала подачи аргона на процесс подогрева при подаче алюминия AAl=142 кг.
Результаты исследования влияния продолжительности подачи кислорода в количестве 1,5 м3 на динамику подогрева металла приведены на рис. 5. Продолжительность подачи кислорода приняли fo2=2 мин. (1 вариант), приняли tO2=3 мин. (2 вариант) и приняли tO2=4 мин. (3 вариант). Аргон подавали сразу после продувки кислородом с расходом 45 м3/час во всех вариантах. Как следует из рис. 5, продолжительность продувки кислородом целесообразно уменьшать.
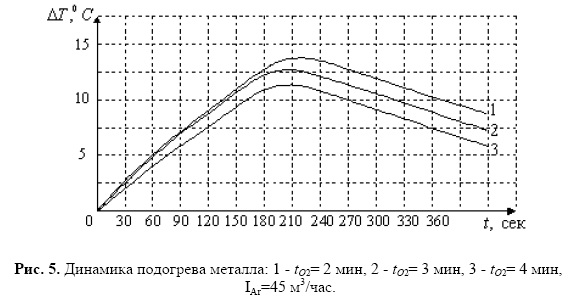
На рис. 6 приведены результаты исследования момента подачи аргона на усреднительную продувку с расходом IAr=45 м3/час. Подача кислорода заканчивалась в момент времени tO2 = 180 сек. Продувку аргоном начинали в момент времени t=0 мин. т. е. с момента ввода алюминия и начала продувки кислородом (вар. 1), t=1,5 мин (вар. 2) и t=3 мин (вар. 3). На рис. 6 видно, что чем раньше начинается продувка аргоном, тем выше подогревается металл. Однако, при этом может уменьшиться усвоение кислорода и эффект подогрева может снизиться. Чтобы этого не произошло, необходимо организовать рациональную гидродинамику жидкой стали в ковше при одновременной подаче аргона и кислорода, как это сделано в работе [3].
На рис. 7 приведены результаты исследования влияния интенсивности продувки аргоном после подачи кислорода в течении 180 сек с интенсивностью IO2 = 0,5 м3/час. Интенсивность продувки аргоном принята IAr=30 м3/час (вар. 1), 45 м3/час (вар. 2) и 60 м3/час (3 вар.). На рис. 7 видно, что при меньшей интенсивности продувки аргоном величина подогрева достигает большего значения и уменьшается со временем с меньшей скоростью. В свою очередь, анализ динамики снижения химической неоднородности по алюминию показал, что одинаковое значение неоднородности 0,46 % достигается к моменту времени 390 с в первом варианте, 360 с во втором и 330 с в третьем. При этом величина подогрева указанных моментов времени составляет 10,511,5 0С. Большее значение подогрева соответствует меньшей интенсивности продувки аргоном. Таким образом, несмотря на увеличение времени усреднительной продувки при меньшем расходе аргона подогрев достигается больше. Однако, учитывая небольшую разницу в значениях подогрева для указанных условий, для сокращения времени усреднительной продувки можно расход аргона увеличивать. Но при этом необходимо принимать во внимание, что увеличение интенсивности продувки аргоном может привести к оголению зеркала металла в ковше.
Таким образом, разработанная математическая модель позволяет разрабатывать и совершенствовать режимы химического подогрева жидкой стали в ковше.
СПИСОК ЛИТЕРАТУРЫ:
1. Кабаков, З.К. Математическая модель химического подогрева жидкой стали в ковше / З.К. Кабаков, П.З. Кабаков // Энергосбережение в теплоэнергетических системах: материалы международной научнотехнической конференции. Вологда: ВОГТУ, 2001, с. 99 102.
2. Святин, А. Г. Определение времени выравнивания состава и температуры жидкой стали в ковше при продувке нейтральным газом / А.Г. Святин, А.Д. Шевченко // Известия АН СССР: Металлы. 1986. № 1.
3. Лившиц, Л.М. Исследование перемешивания металла в ковше в процессе вакуумкислородного обезуглероживания / Л.М. Лившиц, Е. И. Кадинов, В.М. Шифрин, В.Н. Туровский // Известия ВУЗов. Черная металлургия. 1986. № 4.
Библиографическая ссылка
Кабаков З.К., Кабаков П.З., Пахолкова М.А., Сумин С.Н. МОДЕЛИРОВАНИЕ ПРОЦЕССА ХИМИЧЕСКОГО ПОДОГРЕВА ЖИДКОЙ СТАЛИ В КОВШЕ // Современные наукоемкие технологии. 2009. № 7. С. 64-69;URL: https://top-technologies.ru/ru/article/view?id=26496 (дата обращения: 29.08.2025).